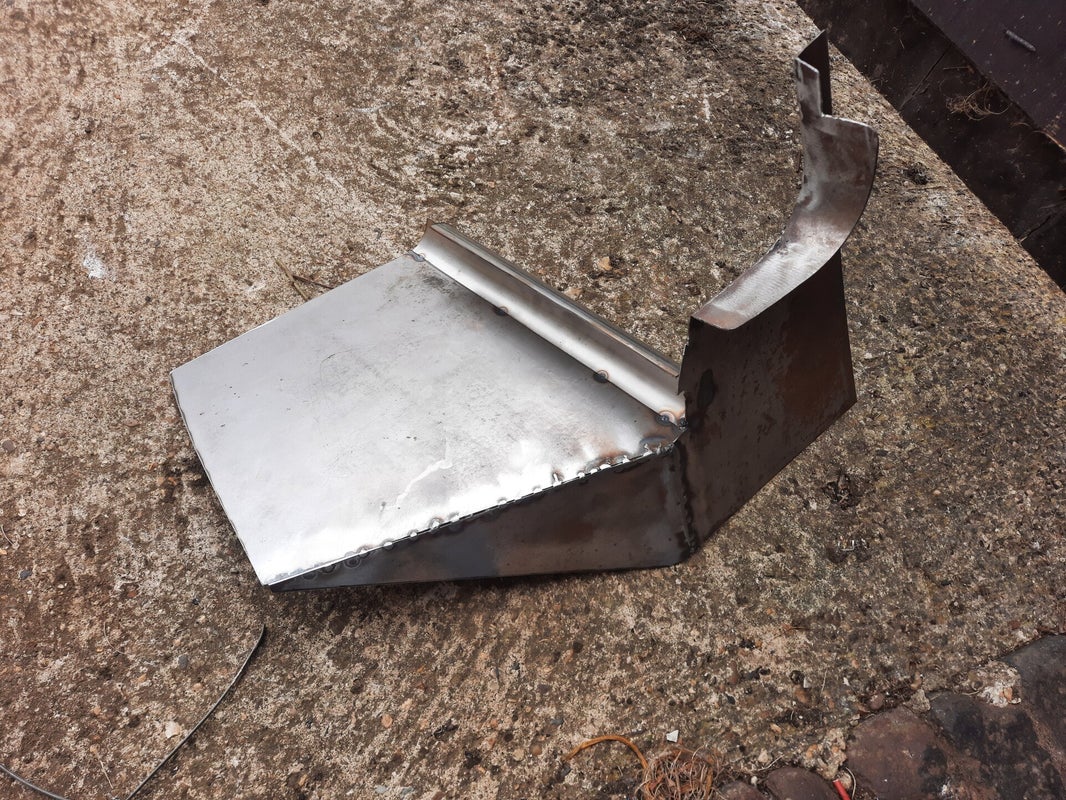
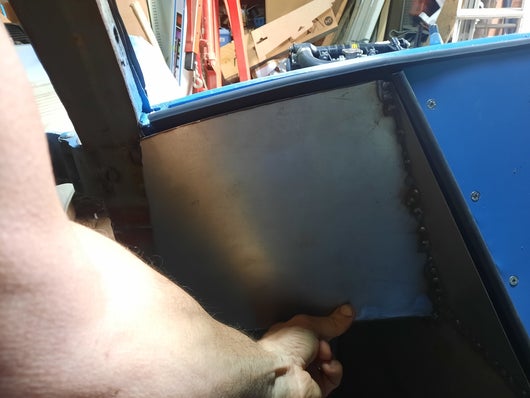
I had to trial fit the panel numerous times as each part got added, there is not a right angle in the whole assembly. Nightmare.

once a bit of primer is on the panels they start looking a bit more complete, the corner has been rounded with filler. I had forgotten to drill the hole for the choke cable - doh!!!
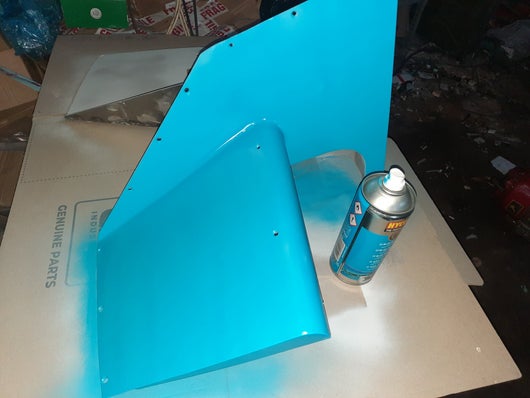
after an application of RAL 5012 paint the panel matches the rest of the car, this is the left hand panel, the most complicated piece of sheet metalwork I have ever attempted.
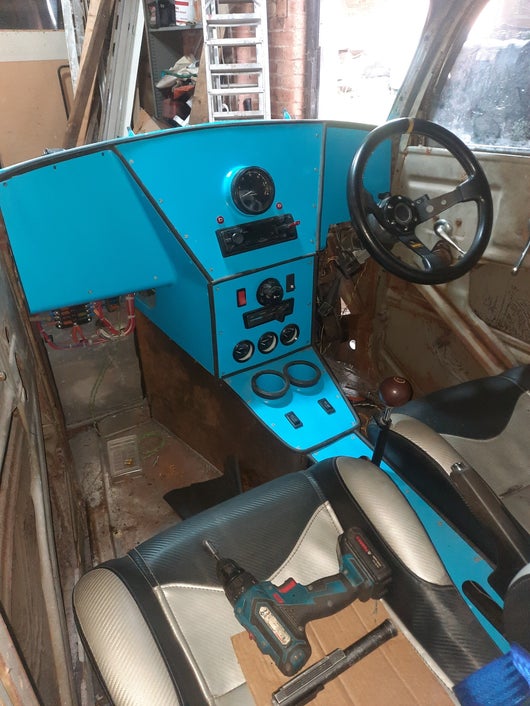
Of all the skills needed to build a car the area I am most lacking in is probably sheet metal work. It's not helped by the fact that I don't really have any sheet metal work tools such as rollers or a folding / bending machine, nor do I have a guillotine, everything has to be cut by grinding discs, jigsaw or tin snips. I do have a very small guillotine but for panels the size I need it's useless. for that reason I have been doing what any normal person would do, I have been ignoring the issue and doing other stuff instead. There has now come the time where I can put it off no longer and have to get on with it.
There are a couple of design considerations, the first being the IVA test and it's associated regulations regarding edges and curvatures, the second one being serviceability, I want removable panels so I can get at the wiring, the heater and all the other gubbins should any repair or service work be required.
The centre panels have already been done, they were dead simple as they are all just flat panels with holes cut or drilled in them, the two side covers are a whole different kettle of fish and are by far the most complicated sheet metal parts I have ever attempted. In preparation I got a gas bottle for my mig welder and have gone from gasless to gas, the results are way better but In fairness I still need more practice. The visible edges are being rounded with filler anyway so a less than perfect weld is not an issue for this job, the unseen welds have been left blobby so they are strong, they can't be seen so I figure that's the way to go. The panels will be painted rather than covered so they have to be very clean and smooth, I figured that welding separate pieces together was the way to go so I don't have to try and hide hammer marks later. IVA demands that the lower edges have to be at least 19mm radius if they are uncovered, that's to protect your knees / legs in an accident. I would have to have a very severe one to bend the car that far but it does seem like a sensible thing. I cut a length of 48mm diameter exhaust pipe in half and used that so my radius is 24mm.
One of the IVA rules that can work for you is that there is an exclusion zone of 127mm around the steering wheel, this is a great place to put things that don't comply with the radius rules, one such thing on my car being the choke knob. To be honest if I had known about this earlier I would have designed the entire dash differently but when I set about it I was not aware of this rule. I think it may have been brought in last May, well after I started my build. I do not recall seeing it in the version of manual I downloaded when I started. Oh well, it's going to be compliant anyway so no harm done.
I am quite pleased with how they have come out, cardboard assisted my design, the angle grinder cut the bits of metal up and the mig joined them back together again, it was all rather splendid. The theme of the 4mm counter sunk allen head bolts used on the other panels will continue so that the panels are removable. As well as hiding everything they also duct the air from the heater in to the footwell, pretty cunning, huh?
It was a lot more enjoyable than I thought it would be, I think because they are quite big chunks that make a big difference to the overall appearance of the car. It's always nice when things take a large, noticeable step forward instead of the tiny unseen bracket that takes 3 hours to make.
I am getting to the point now where the body work will be the next thing, there is an awful lot of it. I need a fibre glass panel for the roof, they are available off the shelf, it's at least a 2 person job to fit it. All 4 doors need repairs at the bottom, they are all rusted out to one degree or other, the sheet metal experience should help here. The running boards need to be fabricated, the fibre glass flip front needs a significant amount of repair / reworking. All the windows need making / fitting, the electric window actuators need fitting, I am thinking of having electric door openers operated by remote control to eliminate the inner door handles but that might be something for down the line, I don't want to add complexity before the IVA test.
The windows represent a bit of a head scratcher at the moment, they have to be of the correct glass and properly marked, getting them made will be very expensive, there is only one company I know of that can do it. The windscreen can be cut down from a Land Rover Defender screen, I guess I could use them for the side screens too but it would take 6 windscreens to do that. I think I will make the none opening side screens and rear screen from appropriately marked perspex, it will be a lot cheaper.
Not yet IVA compliant but it's definitely getting there.
Add comment
Comments