One of the safety critical tests at BIVA - basic individual vehicle approval - is to do with the mounting of the seat belts, all the mounting points have to be in the right places and very, very strong. I think I may have gone a bit OTT with mine but last time I did it there was some discussion as to whether my build was compliant or not, I am not taking any chances this time. I am using 4 point race style harnesses, the upper mounts are in a 40mm square tube with 3mm wall thickness that runs the width of the car. Each end is welded to the original door surrounds, which are triangulated and very strong. I have then added 40mm square uprights that are fully welded to bot the main chassis members and the wheel tubs - they are incredibly strong. 19MM pieces of bar have been drilled and tapped to take 1 1/4 inch long 7 /16 UNF high tensile seat belt bolts - the are not going anywhere. Both ends have been welded to the 40mm square tube, I believe this set up to be stronger than any production car I know of - most use much thinner steel. The lower mounts are fully welded to the transmission tunnel, which is in turn welded to the main 40 x 80mm chassis members. The outer mounts will bolt through the steel floor, 100mm square by 4mm thick steel plates will spread the load.
I am totally confident that the belts themselves would fail long before any of the fixing points, I'm also sure my body would break long before the belts.
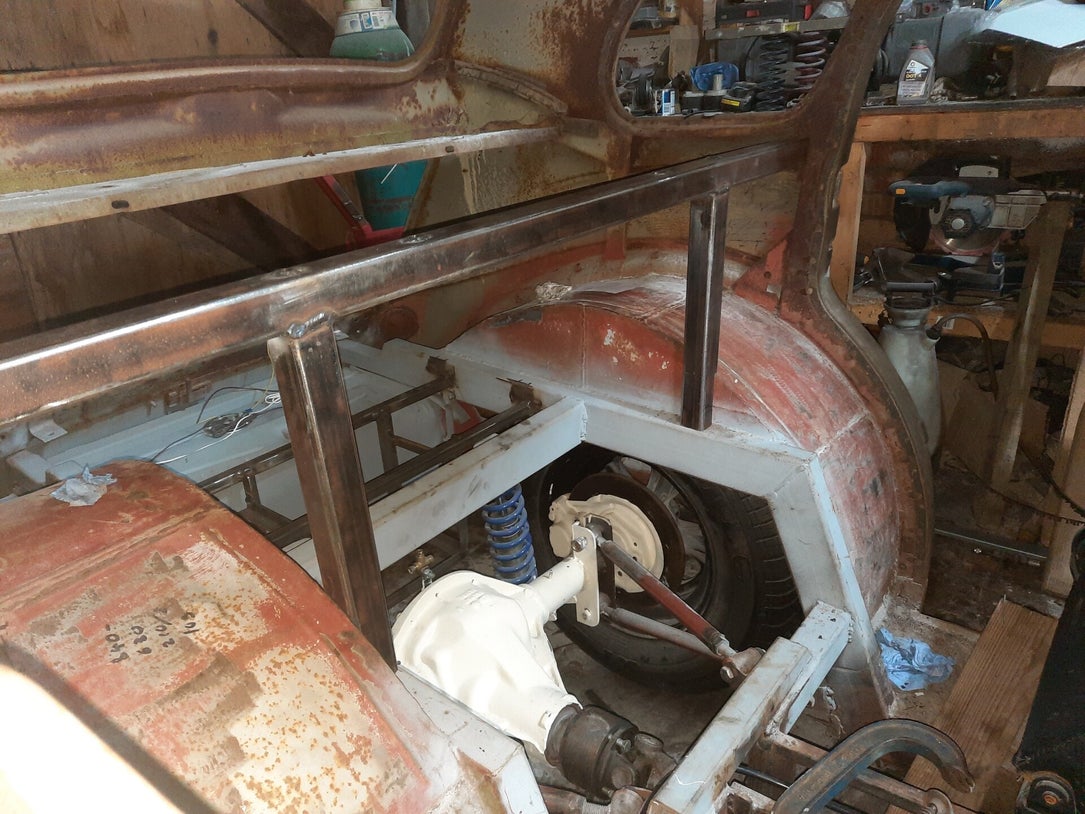
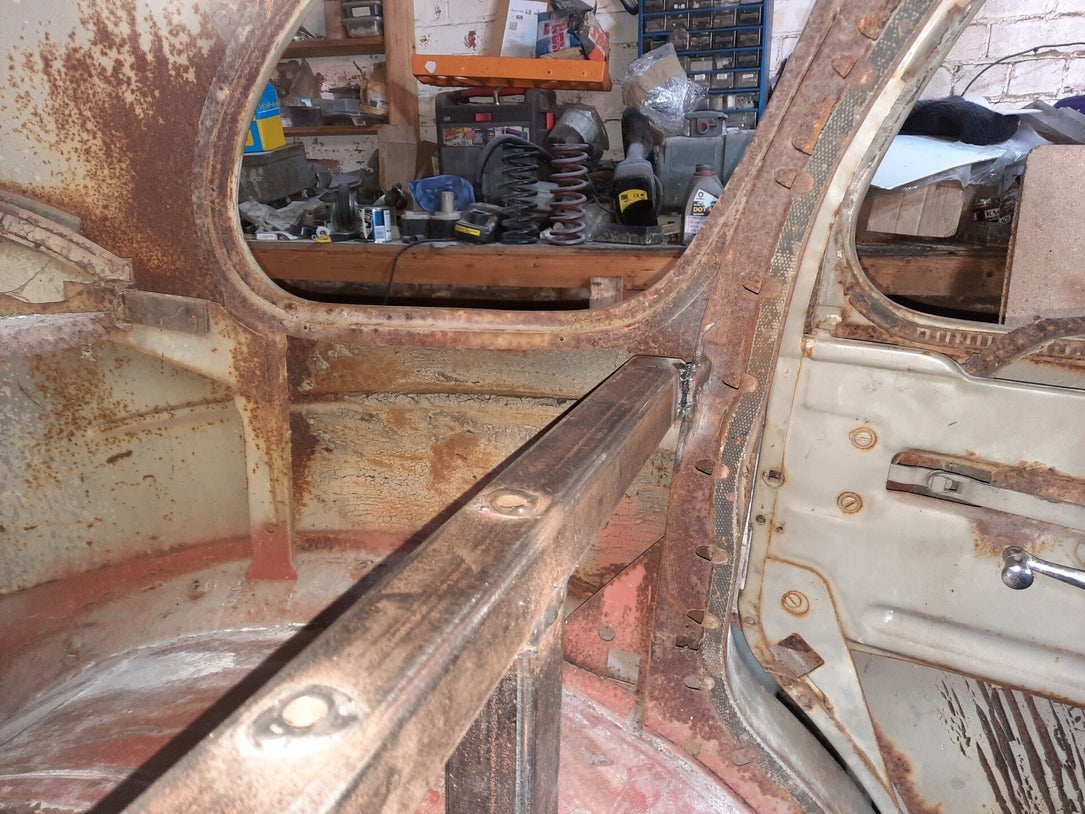
As well as forming the set belt mounts the frame will also support the front of what will be the speaker box. My intention is to build the box out of 18mm marine ply, it should give me excellent sound quality and a very deep, rich bass. I haven't figured out all the specs for that yet, I am thinking a pair of 6 x 9 full range speakers and a single sub woofer of about 10 or 12 inches. I'm not going mad with it, total will only be about 200 Watts, I want it to be top notch sound quality rather than earth shattering power.
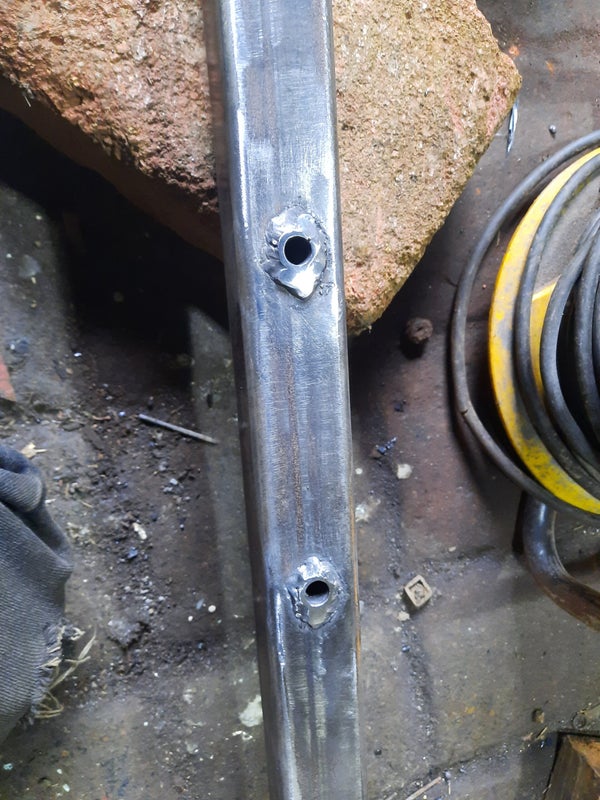
Add comment
Comments